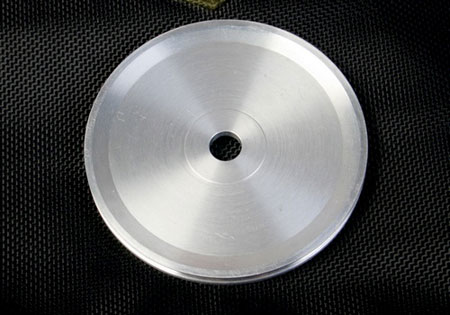
摘要:确定了铁质材料的前处理流程,筛选出一种较好的低温碱性化学镀镍配方,并对镀层的一些性能进行了测试和研究。镀镍工艺优化的结果表明,在40-50℃下可获得光亮、结合力和耐腐蚀性能良好的镀层;一个小时是**佳的施镀时间,一小时后沉积速度将降低。对化学镀镍工艺的影响因素进行了分析讨论。
关键词:化学镀镍,碱性溶液,材料保护,铁质材料。
1.前言
化学镀是利用合适的还原剂,将溶液中的金属离子还原出来,并沉积在经催化活化的镀件表面的一种化学处理过程。对于碱性条件下的化学镀镍过程,可以用以下两个反应式来表示[1]:
[NiL]2++2e- → Ni+L
2Ni+7H2PO2-+H2O –7e-→ 5H2PO3-+2Ni-P+2H2↑+2H+
近年来,化学镀作为一种表面处理技术在工业上日益受到重视。化学镀镍的不断发展归结于该技术具有良好的工艺性,镀层具有独特的物理、化学和机械性能,而且工艺设备简单,易于控制和掌握,镀层均匀平整,适用于复杂形状零件,这些都是电镀技术所不具备的。
目前就大多数化学镀镍工艺来看,其镀覆通常在85-95℃的高温下操作,镀液蒸发快,能量损耗大,次磷酸钠利用率低,pH值变化快,镀覆工艺控制困难。另一方面,高温下操作对有些材料(如塑料等)施镀会造成基体的变形和改性,这些都限制了化学镀的进一步应用,因此,对低温化学镀镍工艺的研究是化学镀研究的一个重要方向。
本研究通过多次试验,对多种镀镍配方进行了筛选,确定了一种快速均匀的镀镍配方;对铁质材料的前处理工艺进行了试验和改进,取得了一定的效果;**后还对镀层的化学和机械性能进行了初步的测试。
2.实验材料、试剂与配方
碳钢棒Φ13×120。
AR试剂:N***4·6H2O,氯化铵,焦磷酸钠,NaOH,柠檬酸三钠,三乙醇胺,丁二酸钠,浓盐酸;CP试剂:NaH2PO2; 工业纯:OP-10。
前处理过程:
除油剂:去污粉
除锈剂:1:1盐酸,活化剂:1mol/l 盐酸。
3.实验结果
(1)工作流程
机械抛光 → 酸洗 → 自来水洗 → 化学除油 → 自来水洗 → 活化→ 自来水洗 → 蒸馏水洗 → 化学镀镍 → 自来水洗 → 蒸馏水洗 → 吹干
(2)镀层厚度以及镀层成分随镀镍时间长短的变化
实验方法:取四支碳钢棒,按上述流程分别镀0.5h,1h,1.5,2h。
然后用70%浓硝酸把镀层****溶解,定容为100ml的溶液,进行光谱(ICP)常规分析,测量其中的Ni,P含量,从而得出Ni的体积,再通过镀层的表面积求出镀层厚度,实验结果如下表2和图1所示:
(4)镀层性能测试
结合力实验按文献[3]的方法进行:
a. 锉刀实验:
试件镀两小时后,用锉刀与表面成45度角方向挫磨试件,镀层没有起皮。
b. 热震实验:
试件镀两小时后,于烘箱中加热至400℃后取出,立即投入室温水中骤冷,镀层没有鼓泡,也没有脱落,有少许裂痕,不仔细观察难以发现。
以上实验表明镀层在酸性和中性介质中均具有良好的耐腐蚀性能。
4.讨论
(1)镀件光亮处理的问题:曾经尝试不对镀件进行光亮处理,而是直接经过去油、酸洗除锈、活化等过程进行化学镀镍,**终****的结果不够理想,表现在:镀层粗糙、不光亮,一段时间后发黄,甚至变黑。其原因在于,镀件表面粗糙不平,经过酸洗以后更难以保证酸蚀过程的均匀性,因此造成覆盖在其表镍层难以平整光滑,光亮度差,而且表面易吸收水分而被氧化显黄色。可见,化学镀镍前对待镀件进行光亮处理是必要的。
(2)洗液与活化液成分和浓度的控制:对于铁材料,一般选用盐酸作为酸洗液。试件经过
去皮后,表面的氧化层已经很薄,所以不宜用太浓的盐酸进行酸洗,酸洗时间也应控制在2-3min,以免因酸蚀不均匀使镀件过度腐蚀变得“千疮百孔”,影响镀层的光洁度,同时也避免了氢脆的影响。
对铁质材料表面进行活化,是为了使镀覆过程更快地进行,所用的盐酸浓度应该更低,因为此时只要求对表面的铁原子进行处理以便使铁与镍反应具有更高的活性,浓度太大会适得其反。
(3)其他的活化方法:将经酸蚀后的镀件置于SnCl2溶液中,使其表面覆盖一层Sn2+,再将镀件在50℃下置于PdCl2溶液中,15min后取出镀件进行化学镀。实验结果是:镀速有明显提高,铁表面冒出大量气泡,但也有明显的缺点就是造成镀液稳定性明显下降,镀完一次后即有Ni覆盖于烧杯壁,严重影响了镀液的使用寿命;另外,从经济角度看,也不科学,操作复杂,成本高,因此我们认为用PdCl2进行表面活化是没必要的。
(4)镀池的洁净:镀池应用蒸馏水反复冲洗后方可使用,贮存镀液的容器更要清洁,由于微量K+、NH4+以及部分的重金属离子均会加速次磷酸钠的分解,同样会影响镀液的使用寿命。
5.结论
实验为低温碱性化学镀镍,整个过程在40-50℃的条件下进行,低温的一个直接后果就是使离子活性降低,扩散速度减慢,氧化还原电位降低,沉积速度大大减小,相比于工业上80-90℃下酸性化学镀镍30-50μm/h的镀速,本实验8μm/h的镀速显得应用价值不大,但低温镀镍却是现在工业上的一个发展趋势,镀速减小的直接原因是能量输入的大大减少,因此寻求新的能量输入方法是解决这个问题的有效途径。目前用于研究的包括超声波、脉冲输入、紫外光输入等。另外,寻求更新更好的加速剂也是一个重要研究方向。
致谢:本文工作****“中山大学实验室开放基金”的资助,在此表示感谢。在实验研究过程中,方北龙老师给我们以精心指导和热情帮助,现代化学技术实验室的老师们为本实验提供了方便,在此向他们表示我们诚挚的感激之情。
参考文献:
[1] 曾建皇,“化学镀镍磷合金机理初探”,电镀与环保,2002. 22(9): 22
[2] 欧阳新平,罗浩江,“低温化学镀镍研究进展”,Electroplating & Finishing,2000. 19(3): 42
[3] 李建三,李异,“低温化学镀镍工艺及镀层性能的研究”,新技术新工艺,2002. 3: 37-40
[4] 闫洪,“化学镀镍工艺的发展和应用”,云南冶金,2001. 30(5): 38-41
[5] Dressick, Walter J, Kondracki J. Colloides and surfaces A, 1996. 108(1): 101-111
[6] Mallory G, Parkwe K. Plating and Surface Finishing,1994. 81(12): 55
[7] Bhatgadde L.G, Joseph.S, Kulkarni S.C. Metal Finishing,1996. 94(4): 45-46
Study on Nickel Electroless Plating on Surface of Iron Materials in Alkali Solution at Low Temperatures
He Jianrong, Zhu Lei, Lin Zhenguang, Wang Xiao, Luo Kai, and Zhang Jilin
(Class 2000, School of Chemistry and Chemical Engineering, Sun Yat-Sen University, Guangzhou 510275)
Superv***r: Fang Beilong, Associate Professor
Abstract:In this paper, a proper plating solution was screened out and the pretreatment flow was confirmed, besides some performances of the coating were tested. It was found that coatings which were bright and good banding could be obtained at 40-50℃. It was also found that the best plating time was one hour because the deposition rate would decrease after that.
Key words:electroless nickel plating, alkali solution, materials protection, iron materials.(end)